اکستروژن
فرآیند اکستروژن را می توان به عنوان فرآیند تولید محصولات پلاستیک توسط پیش راندن مواد از میان یک دای یا دهانه تعریف کرد تا به شکل دلخواه دربیایند. این محصولات که توسط دستگاهی به نام اکسترودر ساخته می شوند می توانند محصول نهایی، و یا غیر نهایی باشند. اکستروژن پلاستیک یکی از رایج ترین روش های شکل دهی پلاستیک ها برای تولید محصولات پلاستیکی و پلیمری مورد نظر می باشد.
در اکستروژن (روزن رانی) یک ماده ترموپلاستیک، ابتدا حرارت مواد را نرم کرده تا آماده شکل دهی شوند. دستگاه اکسترودر این فرآیند را انجام میدهد. این فرآیند نرم شدن Plastication یا Thermal Softening نامیده شده است. رایج ترین توع اکسترودر مورد استفاده، اکسترودر تک پیچ است. این اکسترودر شامل یک دای می باشد که وظیفه فرم دهی محصول پلاستیک را دارد.
در شکل زیر یک برش عرضی از دستگاه اکستروژن پلاستیک (اکسترودر) را مشاهده می کنید که قسمت های مختلف یک اکسترودر و ترتیب قرار گیری آن ها را نشان می دهد. پیچه (Screw) و برل (Barrel) دو قسمتی هستند که مواد پلیمری را حمل می کنند. مواد را ذوب کرده، سپس آن ها را به داخل دای می فرستند. موتور الکتریکی و جعبه دنده پیچه را چرخانده و سرعت آن را تنظیم می کنند. کنترل کننده های دما به المنت های حرارتی یا خنک کننده روی برل متصل هستند تا دما را در نقاطی که توسط کاربر تنظیم شده اند ثابت نگه دارند. طراحی و متعاقبأ توانایی برل و پیچه به موادی بستگی دارد که قرار است اکسترودر مورد نظر برای آن ها استفاده شود.
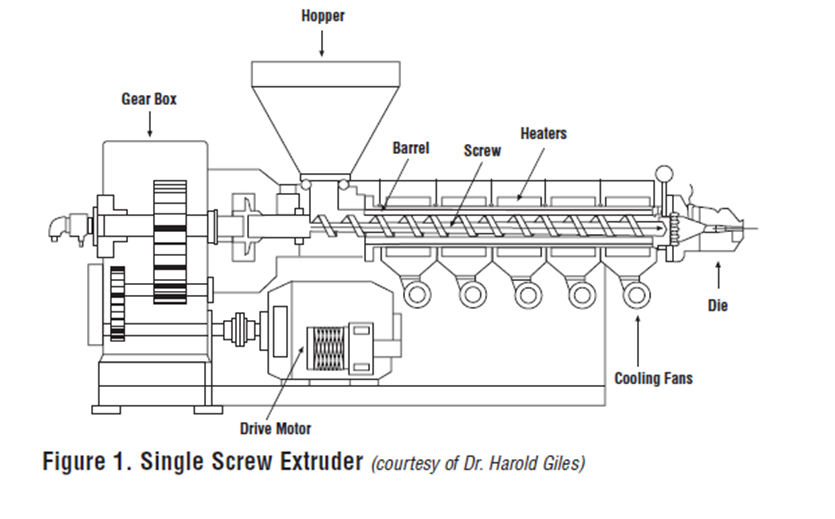
سرعت مارپیچ چرخان به طور معمول تا (Rpm) 120 افزایش پیدا می کند و نیروی ایجاد شده ذرات پلاستیک را به سمت قسمت های جلوی برل هدایت می کند.
مارپیچ از یک سیلندر استیل با یک کانال مارپیچی شکل برش داده شده بر روی آن تشکیل شده است. مارپیچ با چرخش خود داخل برل وظیفه انتقال مواد از قیف ورودی تا دای را ایفا می کند.
نواحی سه گانه مارپیچ:
یک پیچه در فرآیند اکستروژن پلاستیک به طور معمول به سه ناحیه تقسیم می شود. ناحیه تغذیه (Feeding)، ناحیه ذوب (Melting) و ناحیه اندازه گیری یا پمپ (Metering).
ناحیه تغذیه یا Feeding در اکسترودر:
ناحیه تغذیه که مواد را از قیف حمل می کند، از انتهای قیف شروع شده و معمولا عمق ثابتی دارد. طول این ناحیه تابع خواص مواد، هندسه مارپیچ و شرایط فرآوری است. معمولا قسمت تغذیه را در فرآیند اکستروژن پلاستیک شیار دار می سازند تا در راستای محور باعث افزایش اصطکاک شود؛ اما برای عدم افزایش فشار به مقدار بیش از ظرفیت تحمل مارپیچ یا برل، طول این شیر ها باید حداکثر 3/4 برابر قطر مارپیچ باشد.
ناحیه ذوب Compressing در اکسترودر:
در ناحیه ذوب در دستگاه اکسترودر، قطر میله اصلی پیچه به تدریج افزایش پیدا می کند. این ناحیه وظیفه اصلی ذوب پلاستیک را بر عهده دارد. این افزایش تدریجی قطر ماردون سبب افزایش تنش های برشی به مواد می شود و باعث سهولت در ذوب آن ها خواهد شد. ناحیه ذوب نیز از نواحی بسیار مهم در فرایند اکستروژن پلاستیک بوده و طراحی آن بسیار حیاتی می باشد.
ناحیه اندازه گیری یا پمپ Metering در اکسترودر:
ناحیه اندازه گیری در اکسترودر مجددا عمق ثابت نگه داشته می شود. ناحیه اندازه گیری مهم ترین بخش فرآیند اکستروژن پلاستیک و اکسترودر تلقی می شود. فشار کافی برای پمپاژ مذاب پلاستیک را فراهم می کند. قابلیت پمپاژ در بخش اندازه گیری یک اکسترودر تک پیچه تخمین زده می شود. به طور کلی طول ناحیه تغذیه حدود 50 درصد طول مارپیچ، ناحیه ذوب 30 درصد و ناحیه اندازه گیری 20 درصد طول کل مارپیچ می باشد.
مکانیزم جریان مذاب در فرایند اکستروژن پلاستیک:
زمانی که مواد پلاستیک در میان مارپیچ در حال حرکت است با مکانیزم زیر ذوب می شود.
ابتدا یک فیلم نازک از مواد مذاب بر روی دیواره برل شکل می گیرد، زمانی که مارپیچ می چرخد آن را جدا میکند و مواد مذاب را به جلوی پره های مارپیچ انتقال می دهد. زمانی که به هسته مارپیچ می رسد، دوباره جارو می شود و شکل یک حرکت چرخشی را در مقابل لبه پیشانی پره های مارپیچ به خود می گیرد. در ابتدا پره های مارپیچ اکسترودر، شامل گرانول های جامد پلاستیک هستند اما این فرآیند و حرکت های چرخشی منجر به ذوب شدن آن ها می گردد، تا زمانی که منجر می شود به اینکه تنها مواد مذاب بین پره های مارپیچ وجود داشته باشند. زمانی که مارپیچ داخل برل یا محفظه می چرخد، حرکت پلاستیک در میان مارپیچ اکسترودر بستگی به مقدار چسبندگی آن به مارپیچ و برل دارد. در تئوری، 2 حالت بسیار غیر عادی در فرایند اکستروژن پلاستیک وجود دارد. اول اینکه در مواردی مواد تنها به مارپیچ می چسبند و بنابراین مارپیچ و مواد به صورت یک سیلندر جامد درون برل باهم می چرخند. این باعث می شود تا خروجی تقریبا به صفر برسد و مطمئنا مطلوب نخواهد بود. در حالت دوم مواد کاملا روی مارپیچ می لغرند و مقاومت بالایی به چرخش در داخل برل از خود نشان می دهند. این منجر می شود تا مواد فقط حرکت محوری داشته و در واقع ایده آل ترین حالت خواهد بود. ولی در عمل ما حالت هایی بین این دو حالت افراطی را خواهیم داشت. و مواد هم به مارپیچ و هم به برل می چسبند. خروجی مفید اکسترودر نتیجه جریان درگ ایجاد شده از چرخش مارپیچ و ثابت ماندن برل می باشد. این دقیقا معادل جریان یک سیال ویسکوز بین دو صفحه موازی است، زمانی که یک صفحه ثابت و یک صفحه متحرک می باشد. علاوه بر این یک جریان ناشی از اختلاف فشار ایجاد شده در مارپیچ وجود دارد. به دلیل وجود فشار بالا در انتهای اکسترودر، جریان فشار در خروجی کاهش پیدا خواهد کرد. همچنین خالی بودن فضای بین پره های مارپیچ و برل منجر می شود تا مواد به عقب مارپیچ نشت پیدا کرده و به طور قابل توجهی مقدار خروجی را کاهش دهند. این نشتی در مارپیچ های فرسوده بسیار قابل توجه خواهد بود. حرارت و یا سرمای اضافی بر روی اکسترود نیز نقش مهمی در فرایند ذوب پلاستیک ایفا می کند. در اکسترودر ها با قابلیت خروجی بالا، مواد از میان برل به سرعت عبور می کنند، در نتیجه گرمای ناشی از برش برای ذوب آن ها کافی خواهد بود و نیازی به هیتر برل نمی باشد. در این اکسترودر ها به خنک کردن اضافی نیاز خواهد چراکه ممکن است گرمای ناشی از برش در مواد مذاب بیش از حد باشد. در بعضی موارد شاید نیاز باشد که حتی مارپیچ نیز خنک شود. این برای تاثیر گذاری بر ذوب نیست، بلکه به منظور کاهش اثر اصطکاک ناشی از پلاستیک و مارپیچ در فرایند اکستروژن پلاستیک می باشد.
کو اکستروژن (همروزن رانی)
کو اکستروژن پلاستیک ها فرایندی است که در آن تعداد 2 یا بیشتر از مواد مذاب در یک فرایند و یک دای قرار میگیرند و محصولی تشکیل شده از 2 یا بیشتر مواد می سازند. این فرایند هم اکنون در کاربردهای زیادی برای به دست آمدن محصولات چند لایه به کار می رود. در بسیاری از موارد استفاده از یک لایه یا یک نوع پلیمر نتوانست مشتری را از لحاظ ویژگی ها راضی کند پس نیاز به این تکنولوژی حس شد. برای مثال قرار دادن یک لایه رنگی بر روی یک هسته اصلی از مواد با این فرایند قابل انجام است. در صنعت بسته بندی این فرایند بسیار مورد استفاده قرار می گیرد. به عنوان مثال یک پلیمر به عنوان مانع برای رطوبت یا گاز معمولا (PVAL) بر روی پلیمر اصلی قرار میگیرد تا مقاومت به نفوذ رطوبت و گاز در محصول نهایی افزایش یابد.
اکستروژن 2 مارپیچ
در یک اکسترودر ناهمسوگرد دو مارپیچ، نیروی برشی و فشاری اعمال شده به مواد مانند یک کلندر می باشد، یعنی مواد بین دو غلتک غیر هم جهت فشرده می شوند. در یک اکسترودر همسوگرد مواد از یک پیچه منتقل می شود. این نوع از اکسترودر برای پلیمرهای حساس به دما مناسب می باشد چرا که این مواد به سرعت از اکسترودر خارج می شوند. هردو نوع این اکسترودرها مزایا خاص خود را دارند که سبب شده است استفاده از آن ها بسیار مرسوم شود. اکسترودر های ناهمسوگرد برای شکل دهی پلی وینیل کلراید سخت PVC-U و اکسترودر های همسوگرد برای مقاصد کامپاندینگ مورد استفاده قرار میگیرند. دراکسترودرهای ناهمسوگرد کنترل زمان اقامت و دمای مواد، یکسان و راحت است. اگرچه حبس شدن هوا، تولید فشار بالا، حداکثر سرعت پایین مارپیچ ها و خروجی محصول پایین از معایب این نوع فرایند اکستروژن پلاستیک به شمار می رود. اما در اکسترودر های همسو گرد برای پلیمر هایی مانند پلی اتیلن که حساس به دما نیستند، تمیز شدن پیچه ها توسط یکدیگر، سرعت پیچه بالاتر و خروجی محصول بیشتر مشاهده می شود. ماشین های 2 مارپیچ برای فرایند های به خصوص استفاده می شوند، برای مثال جایی که نیاز به آمیزه سازی یک مرحله ای می باشد. این فرایند در مورد پلی وینیل کلراید سخت (PVC-U) صادق است. این مواد در مقابل حرارت پایداری پایینی دارند به همین دلیل در فرمولاسیون آن ها از پایدار کننده های حرارتی پایه فلزی مانند قلع و … استفاده می شود. به دلیل گران بودن این مواد، استفاده از آن ها در مقادیر پایین به صرفه می باشد. یک راه حل مهم برای پایین نگه داشتن مقادیر پایدار کننده حرارتی استفاده از آن و اکسترود کردن آمیزه به صورت همزمان می باشد. اکسترودر های دو مارپیچ این امکان را فراهم میکنند، و به همین دلیل در صنایع لوله و پروفیل های PVC سخت مورد استفاده قرار می گیرند. همچنین درصنایع کامپاند و مستربچ کاربرد فراوان دارند. در شکل زیر شماتیک یک دستگاه دو ماردون را مشاهده می کنید.
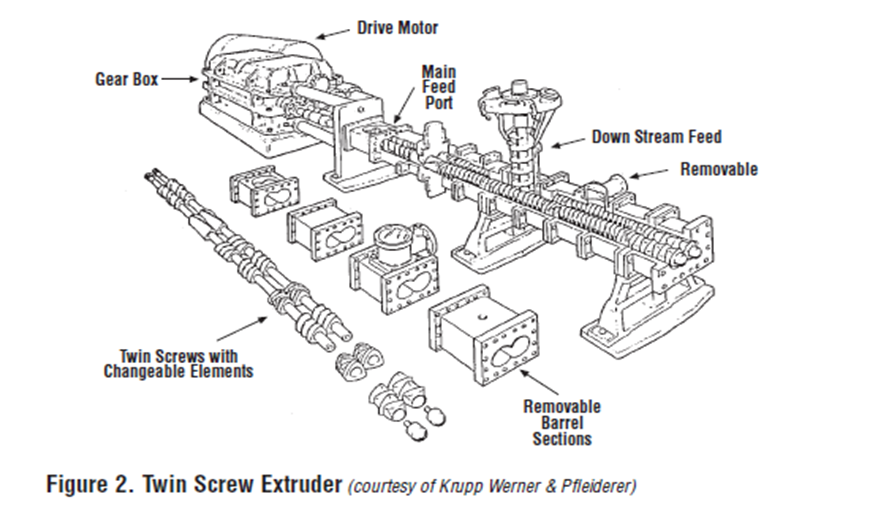